Vlastnosti výroby dřevěných betonových bloků vlastními rukama
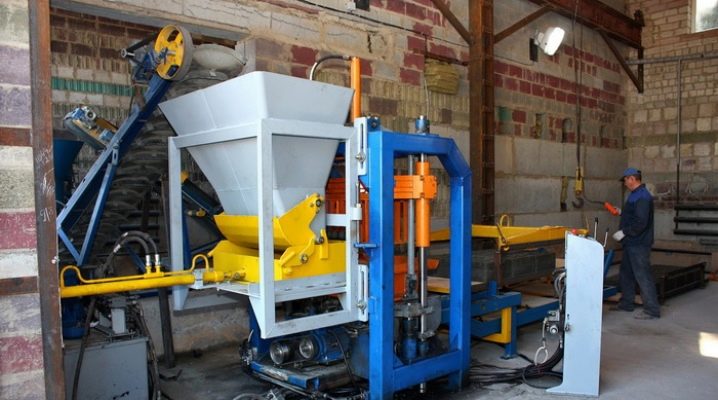
Arbolit je nadšeně popsán v mnoha publikacích, inzerenti se neunaví připisovat mu různé výhody. Ale i když pomineme marketingové triky, je jasné, že tento materiál si zaslouží důkladnou kontrolu. Je dobré vědět, jak na to sám.
Typy a velikosti bloků
Arbolitové panely jsou rozděleny do několika typů:
- velkoformátové bloky (určené pro zdivo hlavice stěn);
- duté výrobky různých velikostí;
- desky pro zesílení tepelné izolace.
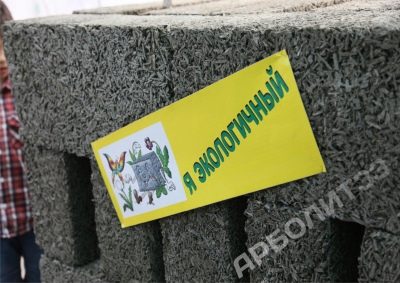
Taky dřevěný beton se používá k výrobě tekutých směsí, kterým se vylévají uzavírací konstrukce. Nejčastěji se však v praxi pod pojmem „arbolit“ rozumí zdicí prvky s nebo bez obkladu. Nejčastěji se vyrábí tvárnice o rozměru 50x30x20 cm.Sortiment se však stále více rozšiřuje a výrobci zvládají nové pozice. Technické vlastnosti vyrobených bloků jsou poskytovány pouze při úplné absenci nečistot.
Prvky s hustotou 500 kg na 1 cu. m. a více jsou tradičně považovány za strukturální, méně husté - určené pro tepelnou izolaci. Lze je použít tam, kde zatížení shora přebírají jiné části konstrukce. Obvykle se hustota měří až poté, co blok ztratil veškerou přebytečnou vlhkost.
Z litého dřevěného betonu o měrné hmotnosti 300 kg na 1 cu. m. stěny lze také postavit, přičemž z hlediska pevnosti nejsou horší než konstrukce z těžšího materiálu.
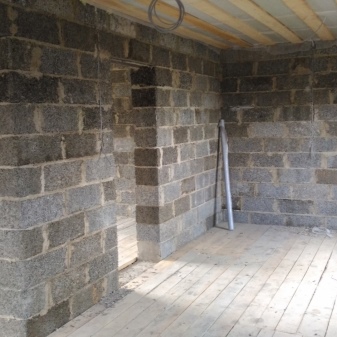
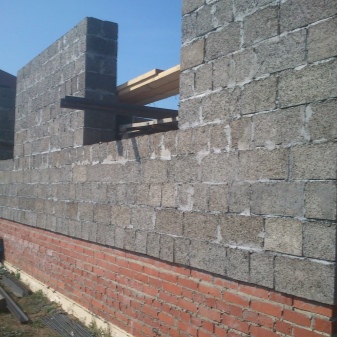
Ke stavbě nosičů stěny jednopatrových domů, jejichž výška nepřesahuje 3 m, je nutné použít tvárnice kategorie minimálně B 1,0... Pokud jsou struktury výše, jsou vyžadovány produkty kategorie 1.5 a vyšší. Dvoupodlažní a třípodlažní budovy by však měly být postaveny z dřevobetonu skupiny B 2.0 nebo B 2.5.
Podle ruské GOST by dřevěné betonové konstrukce uzavírající konstrukce v mírném klimatickém pásmu měly mít tloušťku 38 cm.
Ve skutečnosti jsou stěny obytných budov z bloků 50x30x20 cm rozmístěny v jedné řadě, přísně ploché. Pokud je potřeba vytvořit pomocnou tepelnou izolaci, provádí se tzv. teplý omítkový systém z dřevobetonu... Připravuje se přidáním perlitu a vytvořením vrstvy 1,5 až 2 cm.
Když se prostory nevytápí nebo se čas od času vytápí, použijte metodu zdění na okraji. Tepelně izolační dřevobetonové bloky mají koeficient nasákavosti nejvýše 85 %. U konstrukčních prvků je přípustná hodnota o 10 % nižší.
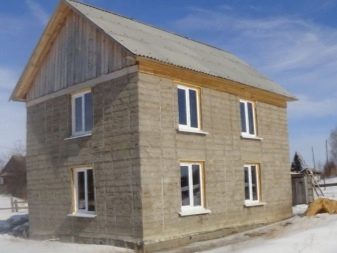
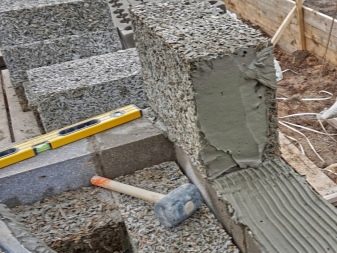
Dřevobetonové bloky je obvyklé rozdělit do tří kategorií podle požární ochrany:
- D1 (obtížně se vznítit);
- V 1 (vysoce hořlavý);
- D1 (nízkokouřové prvky).
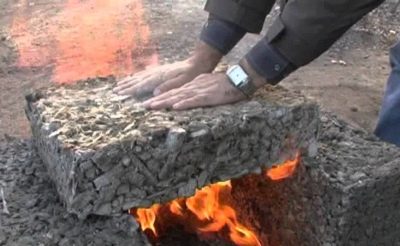
Potřeba vyrábět dřevěný beton doma je z velké části způsobena tím, že stávající výrobci často vyrábějí nekvalitní zboží. Problémy mohou být spojeny především s nedostatečnou pevností, slabým odporem prostupu tepla nebo porušením geometrických parametrů. Bloky jakéhokoli druhu by měly být určitě pokryty omítkou.... Spolehlivě chrání před větrem. S dřevěným betonem se kombinují pouze dokončovací nátěry schopné "dýchat"..
Existuje 6 značek dřevěných betonových bloků, které se liší úrovní mrazuvzdornosti (od M5 do M50). Číslo za písmenem M ukazuje, kolik cyklů přechodu přes nula stupňů mohou tyto bloky přenést.
Minimální mrazuvzdornost znamená, že výrobky by se měly používat pouze pro vnitřní příčky.
Nejčastěji je jejich velikost 40x20x30 cm.V závislosti na zařízení systému drážka-hřeben závisí plocha zdiva a tepelná vodivost stěn.
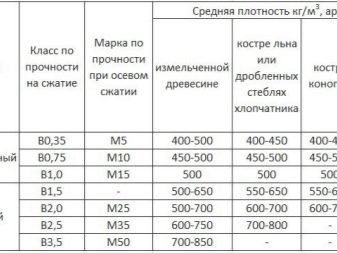
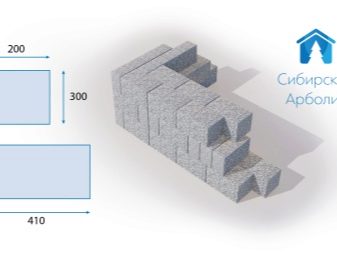
Když už mluvíme o rozměrech a vlastnostech dřevěných betonových bloků podle GOST, nelze než říci, že přísně reguluje maximální odchylky rozměrů. Tak, délka všech žeber se může lišit od deklarovaných ukazatelů o ne více než 0,5 cm... Největší rozdíl úhlopříčky je 1 cm. A porušení přímosti profilů každého povrchu by nemělo být větší než 0,3 cm... Čím vyšší je struktura, tím méně švů bude během instalace a tím menší bude počet švů.
V některých případech jsou nejvhodnější bloky o velikosti 60x30x20 cm, které jsou potřeba tam, kde je délka stěn násobkem 60 cm, což vám umožní upustit od řezání bloků.
Někdy se vyskytuje tzv. "severní arbolit", jehož délka nepřesahuje 41 cm. V některých řadách se při bandážování šířka stěny shoduje s délkou kvádru, v druhé části je součet dvou šířek a švu, který je odděluje.
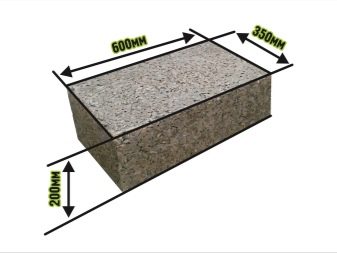
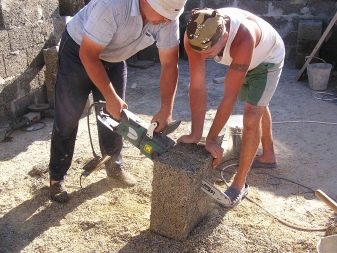
Téměř všichni výrobci vyrábějí přepážkové bloky. V řadě každé společnosti je velikost takových produktů 50% standardní velikosti. Občas se najdou konstrukce o rozměrech 50x37x20 cm, což vám umožní postavit stěny přesně 37 cm, aniž byste se museli uchýlit k obvazování bloků nebo přikládání panelů.
V některých regionech se mohou vyskytovat zcela odlišné velikosti, to by mělo být specifikováno dodatečně. V případě vlastní výroby je třeba je vybrat podle vlastního uvážení.
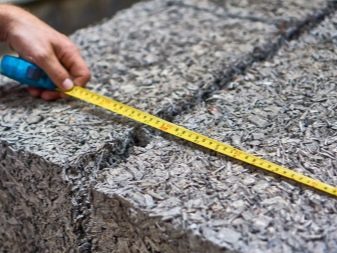
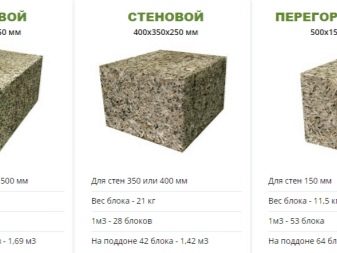
Složení a proporce směsi
Při přípravě výroby dřevobetonových panelů je nutné pečlivě vybrat složení směsi a poměr mezi jejími částmi. Odpad ze zpracování dřeva vždy působí jako plnivo. Ale protože dřevěný beton je druh betonu, obsahuje cement.
Díky organickým složkám materiál dokonale udržuje teplo a nepropouští cizí zvuky. Pokud však dojde k porušení základních proporcí, dojde k porušení těchto vlastností.
Je třeba si uvědomit, že pro výrobu dřevěného betonu lze použít pouze některé typy hoblin. To je jeho podstatný rozdíl od pilinového betonu. Podle současné GOST jsou rozměry a geometrické charakteristiky všech frakcí materiálu přísně regulovány.
Štěpky se vyrábějí drcením neobchodovatelného dřeva. Délka čipů se pohybuje od 1,5 do 4 cm, jejich maximální šířka je 1 cm a tloušťka by neměla být větší než 0,2 - 0,3 cm.
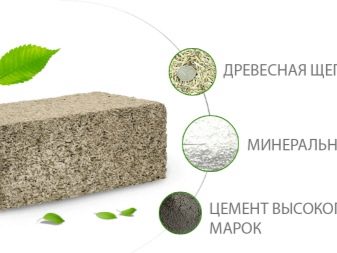
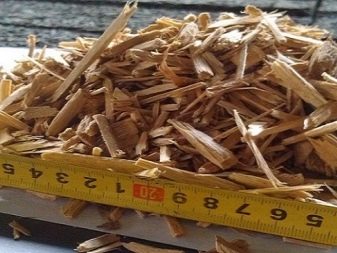
V důsledku speciálního vědeckého a praktického výzkumu bylo zjištěno, že nejlepší dřevěné štěpky:
- tvarem připomíná krejčovskou jehlu;
- má délku až 2,5 cm;
- má šířku 0,5 až 1 a tloušťku 0,3 až 0,5 cm.
Důvod je jednoduchý: dřevo s různými proporcemi absorbuje vlhkost jinak. Dodržení rozměrů doporučených výzkumníky umožňuje kompenzovat rozdíl.
Kromě velikosti je třeba pečlivě vybírat dřeviny. Smrk a buk budou fungovat, ale modřín nebude fungovat. Můžete použít dřevo břízy a osiky.
Bez ohledu na zvolené plemeno je nutné používat antiseptické směsi.
Umožňují vyhnout se výskytu plísňových hnízd nebo poškození surovin jinými patologickými houbami.
Při výrobě dřevobetonu se někdy používá kůra a jehličí, ale jejich maximální podíl je 10, respektive 5 %.
Někdy také berou:
- oheň lnu a konopí;
- rýžová sláma;
- stonky bavlny.
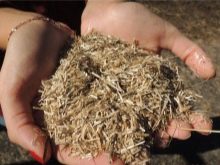
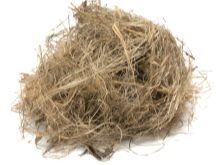
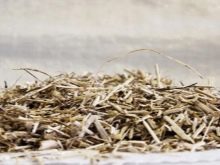
Největší délka těchto součástí je maximálně 4 cm a šířka by neměla být větší než 0,2 - 0,5 cm. Je zakázáno používat vlek a táhnout více než 5 % hmoty použité plnivo. Pokud se použije oheň lnu, bude muset být namočený ve vápenném mléce po dobu 24-48 hodin. To je mnohem praktičtější než 3 nebo 4 měsíce expozice venku. Pokud se k takovému zpracování neuchýlíte, cukr obsažený ve lnu zničí cement.
Pokud jde o samotný cement, Pro výrobu dřevěného betonu se nejčastěji používá portlandský cement... Právě on se k tomuto účelu začal používat před několika desítkami let. Někdy se do portlandského cementu přidávají pomocné látky, které zvyšují mrazuvzdornost konstrukcí a zlepšují jejich další vlastnosti. V některých případech lze také použít cement odolný vůči síranům. Účinně odolává působení řady agresivních látek.
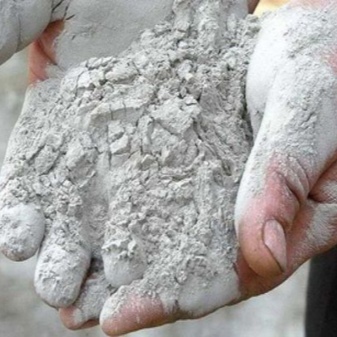
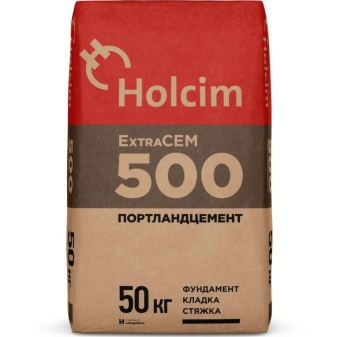
GOST požaduje, aby se do tepelně izolačního dřevěného betonu přidával pouze cement třídy M-300 a vyšší. Pro konstrukční bloky se používá pouze cement kategorie ne nižší než M-400. Co se týče pomocných přísad, jejich hmotnost může být od 2 do 4 % z celkové hmotnosti cementu. Počet zavedených komponentů je určen značkou dřevěných betonových bloků. Chlorid vápenatý a síran hlinitý se spotřebují v objemu nejvýše 4 %.
Stejné je limitní množství směsi chloridu vápenatého se síranem sodným. Existuje také několik kombinací, ve kterých je chlorid hlinitý kombinován se síranem hlinitým a chloridem vápenatým. Tyto dvě kompozice se používají v množství do 2 % z celkové hmotnosti kladeného cementu. V každém případě je poměr mezi pomocnými přísadami 1: 1... Ale aby adstringentní složky fungovaly efektivně, musíte použít vodu.
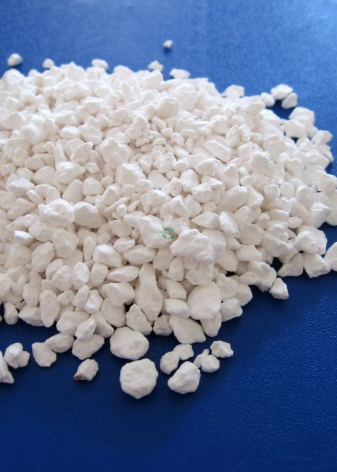
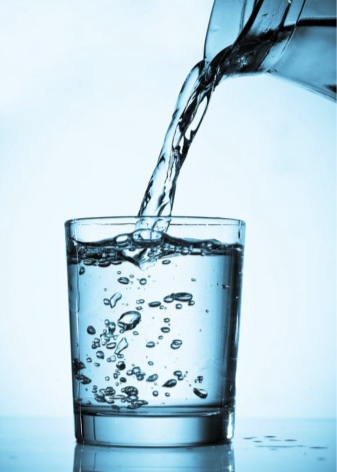
GOST předepisuje přísné požadavky na čistotu použité kapaliny. Při vlastní výrobě dřevobetonu však často odebírají jakoukoli vodu, která je vhodná pro technické potřeby. Normální tuhnutí cementu vyžaduje zahřátí až na +15 stupňů... Pokud teplota vody klesne na 7-8 stupňů Celsia, chemické reakce jsou mnohem pomalejší. Poměr složek je zvolen tak, aby zajistil potřebnou pevnost a hustotu dřevěného betonu.
Výrobky Arbolite mohou být vyztuženy ocelovými sítěmi a tyčemi. Hlavní věc je, že splňují průmyslové standardy.
Norma vyžaduje, aby výrobci testovali připravenou směs dvakrát za směnu nebo častěji, zda vyhovuje následujícím ukazatelům:
- hustota;
- snadný styling;
- sklon k delaminaci;
- počet a velikost dutin oddělujících zrna.
Testování se provádí ve speciální laboratoři. Provádí se pro každou šarži směsi po 7 a 28 dnech po vytvrzení. Mrazuvzdornost musí být stanovena pro dekorativní i nosné vrstvy.
Aby zjistili tepelnou vodivost, měří ji na vzorcích vybraných podle speciálního algoritmu. Stanovení vlhkosti se provádí na vzorcích odebraných z hotových kamenných bloků.
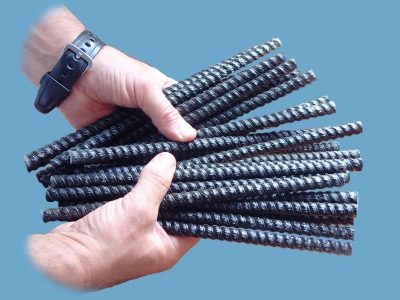
Nezbytné vybavení
Pouze v případě, že jsou splněny všechny požadavky GOST, je možné uvést do výroby určitou značku dřevěného betonu. Ale k zajištění přísného dodržování norem a uvolnění požadovaného množství směsi a následného blokování z ní pomáhá pouze speciální zařízení. Třísky jsou děleny na části pomocí průmyslových brusek. Dále se spolu s dalšími komponentami dostává do zařízení, které roztok promíchává.
Budete také potřebovat:
- přístroje pro dávkování a tvarování dřevěných betonových bloků;
- vibrační stůl, který jim dodá potřebné vlastnosti;
- zařízení na sušení třísek a vařených bloků;
- bunkry, kde se pokládá písek a cement;
- linky dodávající suroviny.
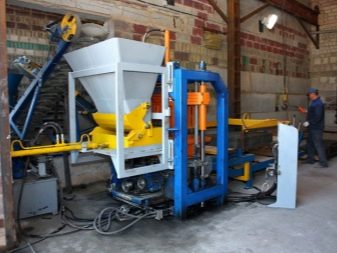
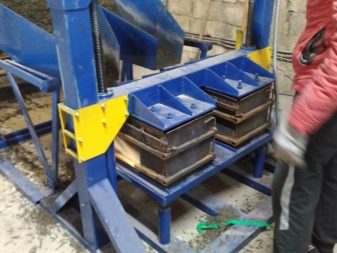
Pokud plánujete vyrábět velké dávky dřevěného betonu, neměli byste používat domácí zařízení. Nejsou dostatečně produktivní, protože ziskovost podniku klesá.
Je užitečné zvážit vlastnosti každého typu zařízení. Zařízení na řezání třísky mají speciální buben s "noži" vyrobený z vysoce kvalitní nástrojové oceli. Navíc je buben vybaven kladívky, která umožňují automatizaci přísunu surovin pro následné drcení.
Aby surovina prošla dovnitř, je buben perforován, je obklopen několika. Větší (vnější) buben stejného tvaru, který zabraňuje rozptylu suti.Obvykle se zařízení montuje na rámy s třífázovými elektromotory. Po naštípání se třísky přemístí do sušičky. Právě kvalita tohoto zařízení nejvíce ovlivňuje dokonalost hotového výrobku..
Sušička je vyrobena také ve formě dvojitého bubnu, její průměr je přibližně 2 m. Vnější buben je perforovaný, což umožňuje přívod teplého vzduchu. Napájení je pomocí azbestové trubky nebo flexibilní ohnivzdorné hadice. Zkroucení vnitřního bubnu umožňuje štěpkům promíchat a zabránit vznícení suroviny. Kvalitní sušení bude schopno uvést 90 nebo 100 bloků do požadovaného stavu za 8 hodin... Přesná hodnota závisí nejen na jeho výkonu, ale také na rozměrech zpracovávaných konstrukcí.
Míchadlo je velká válcová káď. Všechny potřebné suroviny se nakládají z boku a zespodu vychází namíchaná kompozice. Elektromotory a jejich převodovky jsou obvykle umístěny na horní části míchačky malty. Tyto motory jsou vybaveny nožovými sestavami. Kapacita nádrže je dána denní kapacitou linky. Miniaturní výroba nevyrobí za denní směnu více než 1000 vzorů, přičemž se používají kádě o objemu 5 metrů krychlových. m.
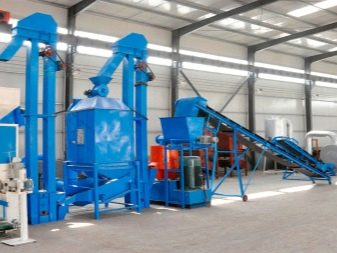
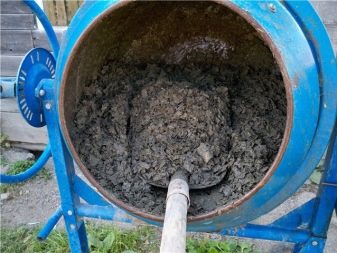
Produkční technologie
Chcete-li připravit dřevěné betonové bloky pro soukromý dům vlastníma rukama, musíte použít 1 díl hoblin a 2 díly pilin (i když v některých případech je preferován poměr 1: 1). To vše se pravidelně řádně suší. Jsou drženy venku po dobu 3 nebo 4 měsíců. Pravidelně štípané dřevo je ošetřeno vápnem, obraceno. Obvykle 1 kubický metr. m. štěpky spotřebují asi 200 litrů vápna v koncentraci 15 %.
Další fáze výroby dřevěných betonových bloků doma zahrnuje smíchání dřevěných třísek s:
- Portlandský cement;
- hašené vápno;
- chlorid draselný;
- tekuté sklo.
Nejlepší je vyrobit si doma bloky o velikosti 25x25x50 cm.... Právě tyto rozměry jsou optimální pro bytovou i průmyslovou výstavbu.
Zhutňování malty vyžaduje použití vibračních lisů nebo ručních pěchů. Pokud není potřeba velký počet dílů, lze použít miniaturní stroj. Speciální tvary pomáhají nastavit přesnou velikost hotového výrobku.
Tváření desek
Nalitím připravené směsi do této formy ručně můžete vyrobit monolitický dřevěný beton. Pokud se přidá vodní sklo, hotový výrobek ztvrdne, ale zároveň se zvýší jeho křehkost. Komponenty je vhodné hníst postupně, ne všechny dohromady. Pak je menší nebezpečí hrudek. Získání lehké konstrukce je velmi jednoduché – do formy stačí vložit dřevěný špalek.
Obrobek je nutné udržovat ve tvaru alespoň 24 hodin... Poté začíná sušení vzduchem pod přístřeškem. Doba schnutí je dána teplotou vzduchu, a pokud je velmi nízká, trvá někdy i 14 dní. A následná hydratace při 15 stupních vydrží 10 dní. V této fázi je blok držen pod fólií.
Aby dřevobetonová deska vydržela déle, neměla by být ochlazována na negativní teplotu. Dřevěný beton v horkém letním dni téměř nevyhnutelně vysychá. Tomu se však lze vyhnout pravidelným postřikem vodou. Nejbezpečnější metodou je zpracování za plně kontrolovaných podmínek v sušicí komoře. Požadované parametry - ohřev do 40 stupňů s vlhkostí vzduchu od 50 do 60%.
Informace o tom, jak vyrobit dřevěné betonové bloky vlastníma rukama, naleznete v dalším videu.
Komentář byl úspěšně odeslán.